防振金具製造部門
防振用金具
独自の生産技術を生かし、車の快適性を作り出していきます。今の車に求められるのは、安全性と機能性、そして快適性です。
静かさと乗り心地の良さを左右するのは、エンジンの振動や走行時のショックを吸収する「防振ゴム」。
ここでは、エンジンやサスペンションに装着する防振ゴムに使用される金具を作っています。
強度や耐久性はもちろん、ゴムとのはまり具合や加工性など、全てにおいて高い精度が要求される部品。
その要求に応えるため、私たちは独自の生産技術を開発しました。
現場で活躍する技術者たちの提案が形となり、大手自動車メーカー各社へと供給。あなたが街で見る車にも、私たちの製品が使われています。
STEP1
材料
鋼材といわれる金属板が防振ゴム用金具の材料となります。
STEP2
タンデムプレス
材料をセットすると、形を作る、穴を開けるなど、加工方法の違うプレス機へと自動で送られ、部品のベースを作ります。
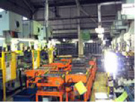
STEP3
溶接
プレスした部品と別の部品を組み付ける工程の作業をここでは行います。ここでは、出来上がった金具にボルトを付けていきます。
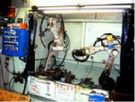
STEP4
メッキ
社外の業者に依頼して、出来上がった製品にメッキをかけていきます。
STEP5
検査
三次元測定器という機械を使い、規格通りに出来上がっているかチェックします。
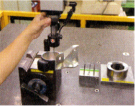
STEP6
完成
検査に合格した製品は、箱詰めして出荷されます。
産業用ホース金具製造部門
高圧ホース用部品
1/100mmの精度を誇る加工技術が、私たちの自信です。
パワーショベルやフォークリフトなど建設機械や工作機械に使われている高圧ホース。
ホースには70kgf/cm²~350kgf/cm²時に2000kgf/cm²もの圧力がかかります。
つまり、私たちが作るホース用金具にも、圧力や温度への耐久性や強度に加え、製品そのものの精度が求められるというわけです。
例えば、生産過程に出来るわずかなバリ(製品からはみ出た不要な部分)がゴム製のホースに亀裂を入れ、圧力や温度によって破れてしまう原因になります。
そこで私たちは、1/100mmの加工精度を誇る生産技術を開発。
ゴムと金属という異なる素材を極限までフィットさせた、質の高い製品を送り出しています。
STEP1
材料
鍛造品を自動供給機にセットします。
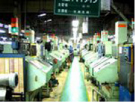
STEP2
切削
自動切削ラインにより、削るなどの加工をしていきます。
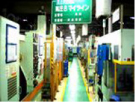
STEP3
メッキ
社外の業者に依頼して、出来上がった製品にメッキをかけていきます。
STEP4
加締
金具にナットとスリーブを取り付けます。
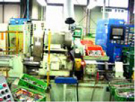
STEP5
検査
金属のパイプを機械にセットします。
STEP6
完成
検査に合格した製品は、箱詰めして出荷されます。
シートベルト金具製造部門
セーフティーパーツ
長年培った金属加工と生産技術のノウハウを結集した新しい事業。
シートベルト部品の中でも、一番重要な役割を果たす「プリテンショナー部品」を生産しています。
海外の大手自動車メーカーも高く評価するその理由は、私たちが誇る「曲げ・プレス・端末を曲げ、穴あけ、成形」といった加工技術力の高さ。
小ロット生産を可能にした「ストレートライン」による、フレキシブルな生産システム。
そして、他社では行われていない「全数検査」という徹底した品質管理体制。
「人命に関わる重要保安部品だからこそ、不良ゼロを目指す」という断固たる企業姿勢も評価されています。
私たちが創業から培ってきた、金属加工技術と生産技術のノウハウを結集して生まれた、まさにオンリーワンといえる新たな事業なのです。
STEP1
材料
金属のパイプを機械にセットします。
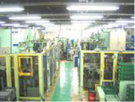
STEP2
PT加工ライン
ここではひとつのラインで、曲げ・プレス・端末を曲げ・穴あけ・成形などをして部品作りをします。
材料をセットするだけで自動生産する独自開発のラインです。
STEP3
メッキ
社外の業者に依頼して、出来上がった製品にメッキをかけていきます。
STEP4
自動機による全数検査
専用の自動検査ラインにより、画像検査および形状検査が行われます。
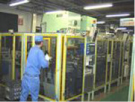
STEP5
完成
検査に合格した物は、箱詰めして出荷されます。